My most recent acquisition is a beauty. She’s a ‘Furnival Jobbing Platen’ or ‘Furnival Jobber’, built in Reddish, nr Manchester. My press is stamped number 1593.
The British Letterpress site has some excellent information about Jobbing Platens in general: There is also some more information about this specific press on this excellent site, along with some history and images.
I am most indebted to the above two sources for invaluable background reading. I spent the days before the collection reading up, searching for other examples of the press and planning a course of attack.
Alas, the best laid plans of Mice and Men and all that…
We arrived in Suffolk in good time, and I gasped appreciatively as we entered the barn (of loveliness), and I saw the press for the first time:

Many things about the press struck me: She’s so graceful – with a solid base reminiscent of the German-built Autovics, and my own Vicobold platen. The sheer weight of the base is perhaps testament to her survival, although, as we embarked upon dissembly we quickly realised that this was a press that has been used lightly and treated well – a glorious thing.
The Furnival brand was clearly visible on the side:

As with my other press collections, we started to gingerly take piece by piece off the base. We unhooked the four rollers, unhinged the throw off lever and unscrewed the feed boards (themselves beautiful wooden pieces):
I was awed by the workmanship and care taken in manufacturing each of these pieces. The cap over the side cogs was stamped ‘CF’ (Charles Furnival) in the inside. I wondered if anyone else had seen those letters in c.150 years. (This part is the red cap visible in the photos below).
We unscrewed the flywheel, gently rolling it outside. This alone was incredibly weighty.
One of the things that struck me again was the need to know which bits needed unscrewing, which needed a gentle tap with a hammer and which needed tugging out with sheer strength and perseverance.
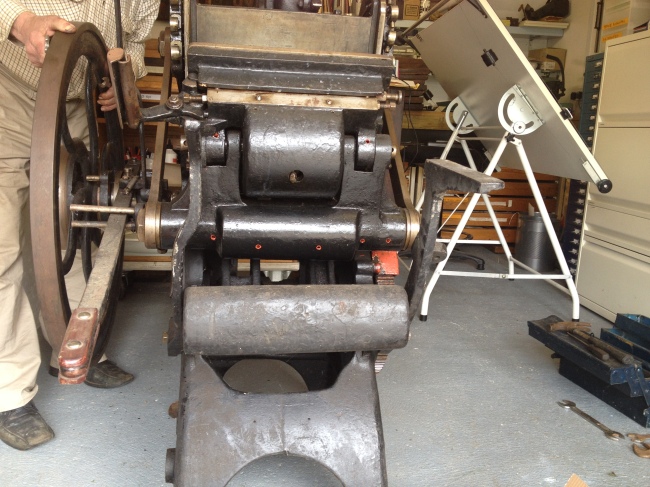

One of my favourite parts of the mechanical jigsaw was the heavy side sections which held the rollers in place. They looked like harps, or tridents. In the end we only removed one of these, as the side bars were positioned so specifically. I have a bit of a theory, which involves dissembling as little as possible: enough for safety and transportability, but not so much as to mess with engineering and precision that has managed for over a century.
This next image shows the side sections and side bar in position:

With all the moving sections removed, the press was looking very bare and we had a growing pile of parts. It can be a good idea to draw a simple diagram and number everything, so you know what goes where when you come to reassemble. As it was, I just took a million photos on my iPhone, and made sure we kept all the bolts, springs, screws and washers in a distinct box, so none were lost (hopefully):

And this is where things started to go awry. I mean, not disastrously. At no point were we edging a press out from under an angry wasps nest, only to find it was too heavy for the tail lift, and then holding it up at great personal danger to life and limb. (No, the Vico pick up still retains the title for Most Mortal Danger Encountered.)
Even with all the external pieces removed, the platen base was super, super heavy. (300-400kg perhaps):

With a winch we could move the press forwards, and with some concerted effort we managed to spin it round, but it became quickly apparent that tipping it sideways to travel was not going to be easily achieved. At this stage I felt like we had come too far to risk shattering the base by doing anything risky.
The possible solutions at this stage included something to do with an engine crane, (which we didn’t have), or the good old tail-lift and pallet truck option. I have to admit that, at this stage, my cool unflappable veneer slipped quite a bit. My love of the press was matched by a bit of exhaustion, desperation, embarrassment, and a failure of pragmatism. Also, our chocolate supply had melted.
Minor meltdown surpassing, after a bit of a chat with the previous owner of the press, (who was unswervingly welcoming, patient and friendly), we decided to do the latter.
So this post is a bit of a story in progress, I guess. I’ll report back in a couple of weeks as to how trip two to Suffolk goes.